- Home
- India
- World
- Premium
- THE FEDERAL SPECIAL
- Analysis
- States
- Perspective
- Videos
- Sports
- Education
- Entertainment
- Elections
- Features
- Health
- Business
- Series
- In memoriam: Sheikh Mujibur Rahman
- Bishnoi's Men
- NEET TANGLE
- Economy Series
- Earth Day
- Kashmir’s Frozen Turbulence
- India@75
- The legend of Ramjanmabhoomi
- Liberalisation@30
- How to tame a dragon
- Celebrating biodiversity
- Farm Matters
- 50 days of solitude
- Bringing Migrants Home
- Budget 2020
- Jharkhand Votes
- The Federal Investigates
- The Federal Impact
- Vanishing Sand
- Gandhi @ 150
- Andhra Today
- Field report
- Operation Gulmarg
- Pandemic @1 Mn in India
- The Federal Year-End
- The Zero Year
- Science
- Brand studio
- Newsletter
- Elections 2024
- Events
Blue Pottery Heritage: The Persian technique that India made its own
When a strand of cobalt-blue silk unspools across centuries and continents, it braids two great stories: the luminous ceramics of Persia and the azure pottery of Jaipur, each conceived from a hop of cultures along the world's fabled trade routes. Originating in the Islamic golden age (8th-13th century), Persian blue pottery was introduced to India by Turkic artisans who accompanied...
When a strand of cobalt-blue silk unspools across centuries and continents, it braids two great stories: the luminous ceramics of Persia and the azure pottery of Jaipur, each conceived from a hop of cultures along the world's fabled trade routes. Originating in the Islamic golden age (8th-13th century), Persian blue pottery was introduced to India by Turkic artisans who accompanied invading armies pushing into the subcontinent. Historically, the art of blue-glazed pottery was an imported technique.
Mongol artisans fused Chinese glazing methods with Persian decorative motifs, a tradition that was later introduced to India by Muslim craftsmen in the 14th century. Under the Mughal rulers, the craft gained prominence as an architectural embellishment, inspired by the grand structures of Samarkand. Over time, Kashmiri potters adopted the technique, which gradually made its way to the plains of Delhi.
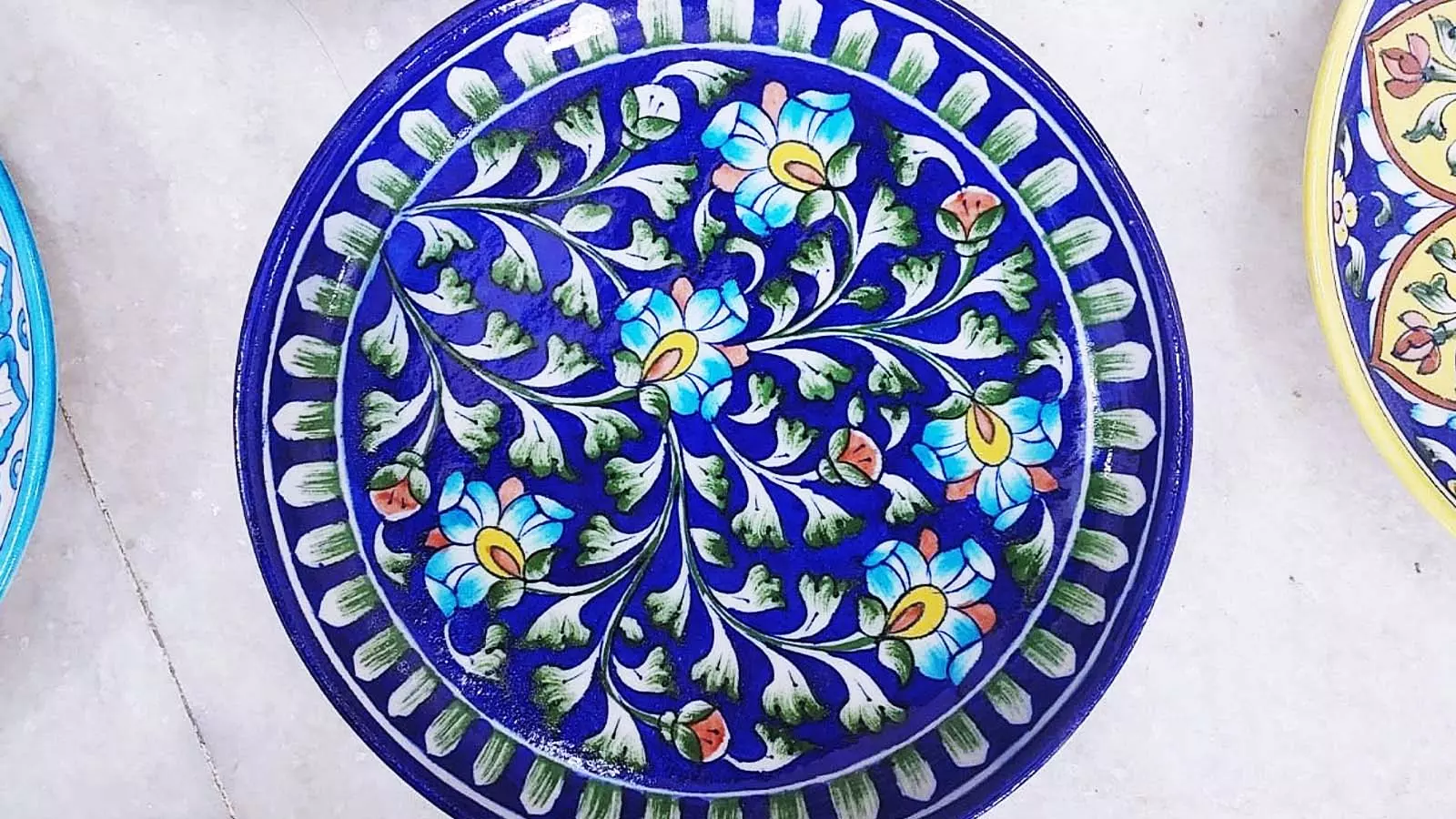
Persian blue pottery was introduced to India by Turkic artisans who accompanied invading armies pushing into the subcontinent.
The craft, which flourished under Mughal patronage, was once believed to serve a more utilitarian purpose—detecting poisoned food. As author Amar Tyagi notes in his book Let's Know Handicrafts of India, “Mughal kings used blue pottery to check their food. If the colour of the glaze changed, it conveyed that the food had been tampered with, or poisoned.” Today, Delhi, Rampur, Jaipur, and Khurja are renowned for their blue pottery traditions, each with its distinctive method. “Jaipur and Delhi follow a method where first the basic forms are created, then painted on the surface, and finally covered with finely ground glass before being baked in the fire,” Tyagi explains. “Meanwhile, potters in Khurja and Rampur prepare the base from red clay, which is then fired.”
In Rajasthan, blue pottery found royal favour. Maharaja Sawai Ram Singh II of Jaipur (r. 1835–1880), an ardent patron of the arts, played a pivotal role in its resurgence. He established a school of art in Jaipur, inviting skilled craftsmen to settle in the city. The legacy of his patronage is evident in the city’s architecture, from the striking blue-tiled fountain at Rambagh Palace to the extensive use of blue-glazed tiles in Jaipur's construction. By the late 19th century, Jaipur had emerged as the epicentre of a thriving blue pottery industry, adapting traditional Persian designs to cater to an evolving, sophisticated clientele. “Once limited to urns, vases, and jars, blue pottery has since expanded its repertoire. Today, artisans craft tea sets, cups, plates, jugs, ashtrays, and even napkin rings, ensuring that this centuries-old tradition remains an integral part of India's artistic heritage,” writes Tyagi.
As Dr. Leela Bordia notes in her book Jaipur Blue Pottery: A Tribute, the art form has endured significant highs and lows over its nearly 200-year history. The influence of Mughal aesthetics on Rajasthan's artistic and architectural landscape is undeniable.
“From the medieval period onwards, close contact between the Rajputs and Mughals led to the Mughal style becoming deeply embedded in Rajput forts, palaces, customs, cuisine, attire, jewellery, and crafts. Despite its early prominence, Jaipur’s blue pottery faced periods of decline, at times teetering on the brink of extinction. However, dedicated individuals and organizations worked to revive the dying art, ensuring its survival and resurgence. Today, blue pottery is a thriving industry, sustaining the livelihoods of thousands of artisans and continuing to captivate collectors and connoisseurs worldwide,” writes Bordia.
In the village of Kot Jewar, 40 km from Jaipur, the ancient art of blue pottery has become the lifeblood of the community. This settlement, now synonymous with Rajasthan's iconic cerulean crafts, reveals its artistic heritage across sun-drenched terraces of the village, where these blue creations claim space on rooftops and courtyards of artists' homes, absorbing the abundant sunlight as part of their careful drying process. Vimal Prajapat, a 25-year-old artisan at Ramnarayan Blue Art Potteries, continues his family's legacy in Jaipur’s renowned blue pottery tradition. “The term ‘Blue Pottery’ originated from the blue dye used in its early days,” he explains. “Its delicate nature comes from a unique production process—glazed and fired at low temperatures using a faience-like frit material.”
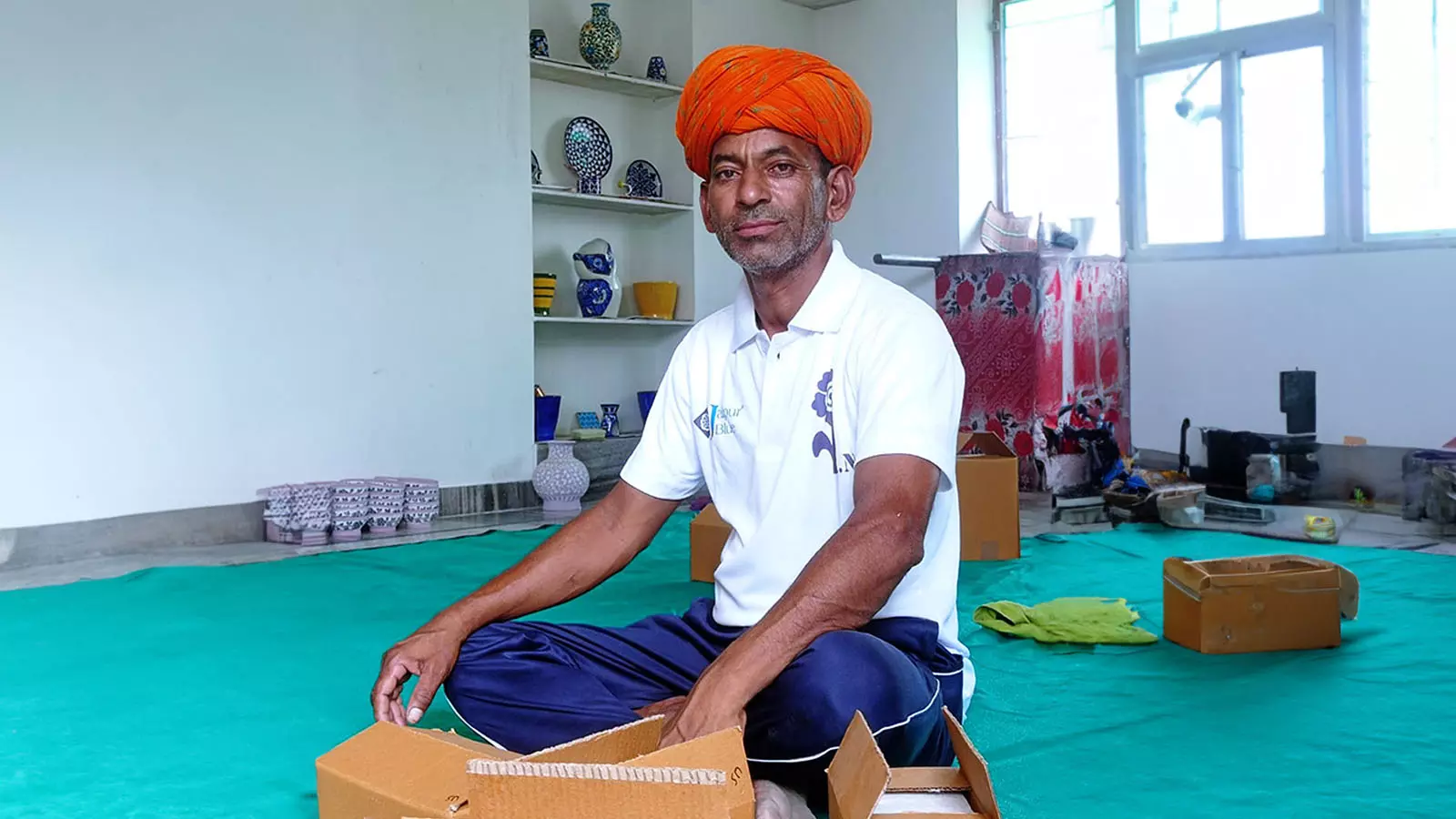
Ramnarayan Prajapat’s journey from hardship to recognition is a journey of solidity and innovation.
While both Persian and Indian pottery share the signature combination of cobalt blue on white backgrounds, each has its own artistic identity. “Over a common foundation—lightweight, translucent, quartz-based vessels—Persians tend to incorporate a broader palette, combining various shades of blue with turquoise and emerald tones. In contrast, Jaipur pottery achieves its bold cobalt blue, through copper oxide. Persian pieces typically showcase Islamic geometric patterns and flowing calligraphy, whereas Jaipur pottery embraces Indian designs—peacocks, native flowers, and regional motifs. The signature palette features cobalt oxide-derived blues, greens, and whites, with occasional touches of yellow and brown,” explains Prajapat.
Vimal is soon joined by his father, Ramnarayan, a renowned blue pottery artisan, who reflects on his family's journey and the evolution of their craft. Ramnarayan, who secured significant orders, including 40,000 pieces for clients in the US and UK and 200 for the Taj Mumbai, carved a new path for his village. “My father was a farmer, and like many in our impoverished village, we struggled. But I, an eighth-grade dropout, left home at 15 to learn blue pottery in Jaipur and Jodhpur.” he recounts.
His son Vimal promptly adds, “When he returned, he didn’t just bring back a craft—he changed our village’s destiny.” Ramnarayan’s journey from hardship to recognition is a journey of solidity and innovation. Forced to start working at 15 to support his family, he turned to pottery as a means of survival. On August 20, 1980, he founded Ramnarayan Blue Art Potteries as a modest bootstrap venture. Over the years, they participated in numerous government and SME training programs, successfully generating returns on the family’s initial investment. In 2019, their efforts were nationally recognised when their pottery shop was named India’s Best Brand in a government-sponsored competition.
As he puts the finishing touches on a commissioned piece, Ramnarayan takes a moment to guide us through the intricate process of blue pottery. The craft of blue pottery relies on a set of traditional tools and raw materials that have remained largely unchanged over time. Essential tools include the Chakki (grinder) and a small grinding stone for refining raw materials, the Jaali (iron sieve) for sifting, and molds of various shapes and sizes. Artisans use the Tarazu (weighing tool) for precise measurements, a fired clay flattening tool, and a Base Stone Block for smoothing surfaces. Other key instruments include Regmaal (sandpaper in 60, 100, and 180 grades), the Patti (iron blade/knife), Saancha (iron cutter), Koochi (broom), Chaak (potter’s wheel), brushes, and the Bhatti (heating kiln). The process also involves Patiya (cement plates) and Nali (terracotta stands) to support and shape the pottery.
The raw materials used in Jaipur’s blue pottery are equally distinctive and eco-friendly. The base mixture consists of ground quartz stone, Kaanch (glass), Katira Gond (edible gum), Multani Mitti (Fuller’s Earth), Saaji (soda bicarbonate), and Maida (flour), which is used for coating and occasionally as a substitute for Fuller’s Earth.
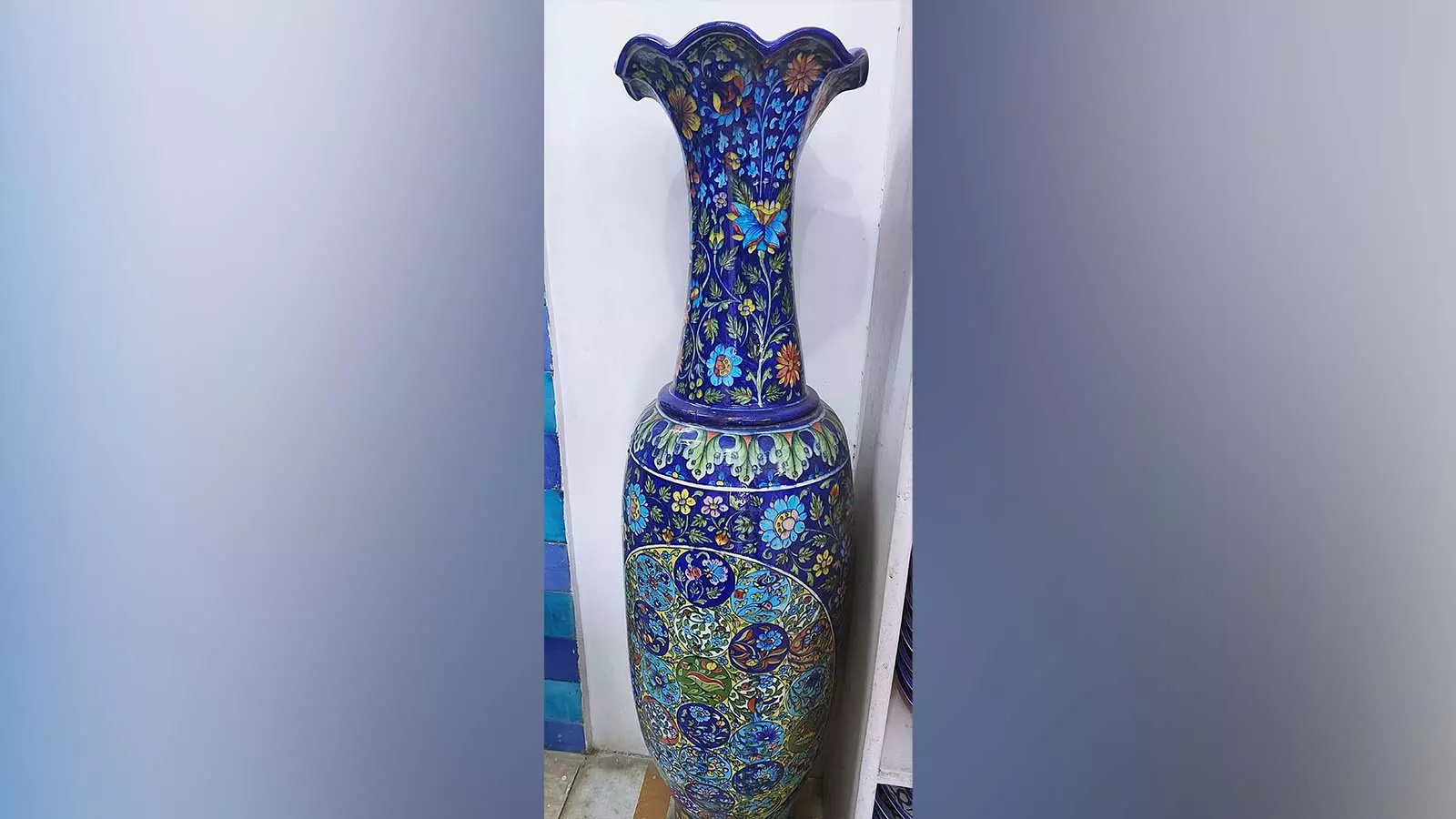
The raw materials used in Jaipur’s blue pottery are equally distinctive and eco-friendly.
“This is the only art form where pottery is created without using clay. Instead, we work with a mix of gum, water, fuller's earth (Multani Mitti), and quartz powder,” Prajapat shares, elaborating, “The process is both intricate and time-intensive. We begin by preparing a moulding dough from these core ingredients. This is rolled and flattened into a 5-mm-thick 'flatbread,’ which is then placed into moulds filled with a blend of fine stones and ash from burnt wood.” Once the mould is inverted and removed, the shaped dough is set aside to dry. The pottery is then cleaned, shaped, and polished with sandpaper before being immersed in a solution of powdered glass, quartz powder, refined flour, and water.
“After drying, we decorate the surface using a mixture of cobalt oxide and edible gum, applying colours made from other metal oxides. These oxides are crushed on stone and brushed onto the pottery,” he adds. Jaipur’s blue pottery relies on two primary types of pigments—oxide colours and ferro colours. The signature colours of blue pottery come from distinct metal oxides: cobalt oxide produces deep blue, copper oxide creates light blue, chrome oxide results in green, cadmium oxide yields bright yellow, and ferro colours generate shades of brown. In the molding stage, Raakh (burnt wood dust) plays a crucial role in shaping the product, as it is non-sticky and easily removed once dried.
The firing process relies on locally sourced, seasoned Khezadi wood, while other essential ingredients include charcoal, water, borax powder, zinc oxide, potassium nitrate, and boric acid—each contributing to its unique texture. Traditionally, lead was used in the glaze, but modern techniques have shifted towards lead-free coatings, ensuring a more sustainable and eco-friendly production process.
Creating a single piece of blue pottery takes around 15 days to complete, whether it’s a single plate or a batch of one hundred. “This is due to the intricate, multi-stage process involved,” Prajapat explains. “From preparing the dough and crafting molds to casting, scrubbing, finishing, attaching the base, smoothening, designing, colour mixing, painting, glazing, and finally firing, each step requires precision and expertise.”
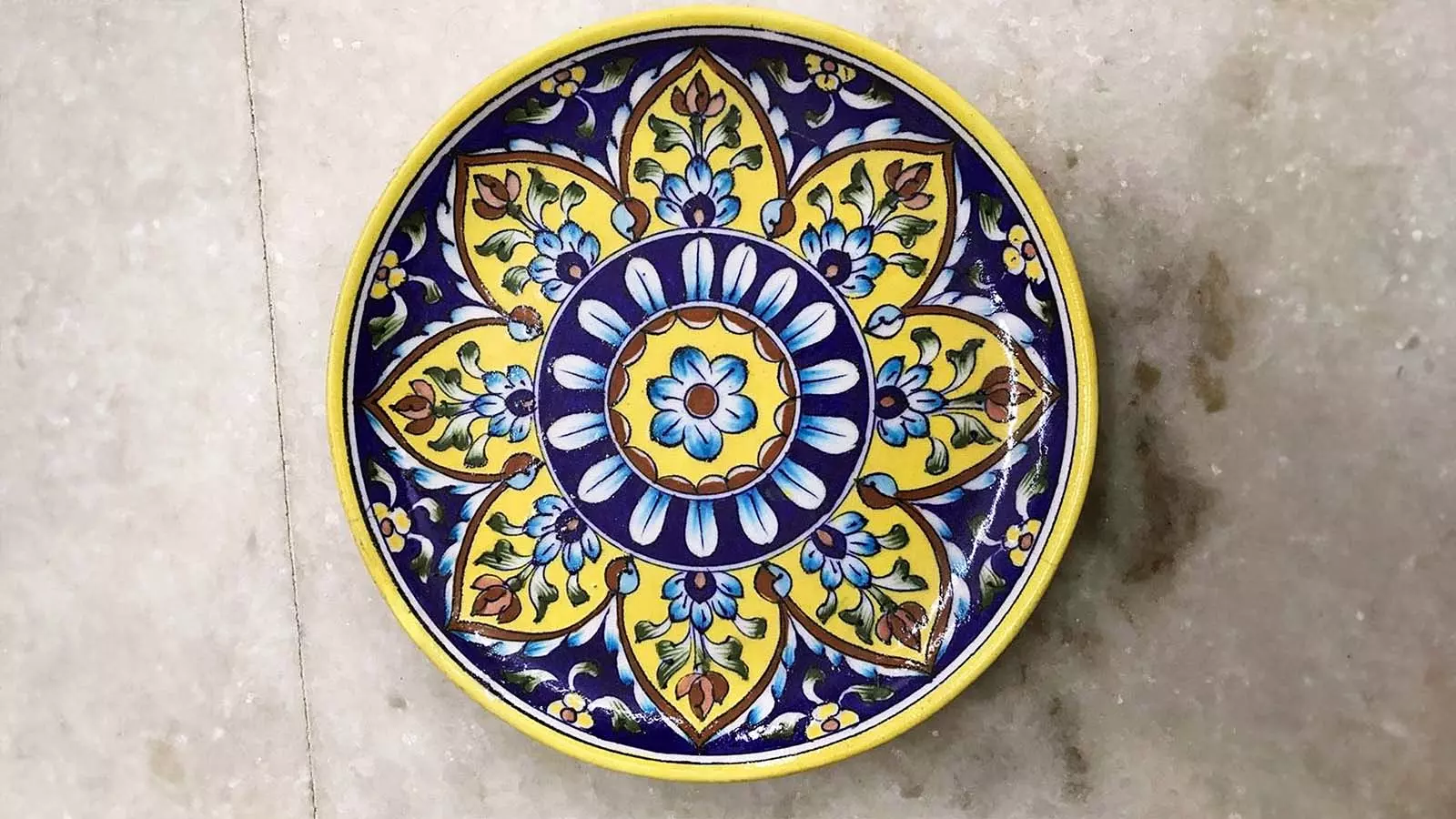
The signature colours of blue pottery come from distinct metal oxides: cobalt oxide produces deep blue, copper oxide creates light blue, chrome oxide results in green, cadmium oxide yields bright yellow, and ferro colours generate shades of brown.
Besides, the craft comes with challenges, including a high damage ratio of 30–40%. While materials can be reused if damage occurs before firing, any post-firing breakage means starting from scratch. Despite these hurdles, the Prajapat's consistently meet deadlines, driving remarkable growth for their family-run business. Production halts during the monsoon, as the traditional technique relies on sun-drying, making work impossible during the rainy season. Reflecting on the shifting landscape of their blue pottery enterprise, Prajapat notes the impact of recent years on artisan employment. “Before the pandemic, we collaborated with 300–400 rural artisans, including 50–70 women, to craft these ceramics. Today, only 100 artisans remain employed full-time, while many have transitioned to working as independent contractors. For large orders, we partner with these contractors, supply them with raw materials, and coordinate to complete the work efficiently,” he explains.
Despite these challenges, Jaipur’s blue pottery—recognized with a Geographical Indication (GI) tag—continues to be a sought-after craft. As Swasti Pachauri writes in her collection of essays, 'Reflections: Handicrafts, Sustainability, and Livelihoods,' “Popular in crockery, décor, artefacts, and other utility items, Jaipur Blue Pottery finds a place in almost every clay aficionado’s household.”
Yet, a word of caution comes from author Dave Abram in 'The Rough Guide to India,' where he highlights Jaipur as a prime destination for blue pottery enthusiasts. He recommends exploring the outlets along Amber Road for traditional Persian-influenced vases, tiles, plates, and candleholders. For those seeking top-quality craftsmanship, he points to the shop of Jaipur’s renowned ceramist, Kripal Singh, located at B-18 A Shiv Marg, Bani Park, near the Jaipur Inn. However, Abram warns buyers that Jaipur’s blue pottery is primarily decorative, stating, “None of it—despite what some shop owners claim—should be used for hot food, as the glazes are unstable and potentially toxic.”