- Home
- India
- World
- Premium
- THE FEDERAL SPECIAL
- Analysis
- States
- Perspective
- Videos
- Sports
- Education
- Entertainment
- Elections
- Features
- Health
- Business
- Series
- In memoriam: Sheikh Mujibur Rahman
- Bishnoi's Men
- NEET TANGLE
- Economy Series
- Earth Day
- Kashmir’s Frozen Turbulence
- India@75
- The legend of Ramjanmabhoomi
- Liberalisation@30
- How to tame a dragon
- Celebrating biodiversity
- Farm Matters
- 50 days of solitude
- Bringing Migrants Home
- Budget 2020
- Jharkhand Votes
- The Federal Investigates
- The Federal Impact
- Vanishing Sand
- Gandhi @ 150
- Andhra Today
- Field report
- Operation Gulmarg
- Pandemic @1 Mn in India
- The Federal Year-End
- The Zero Year
- Science
- Brand studio
- Newsletter
- Elections 2024
- Events
What bone, marble and glass in Udaipur tell us about the forgotten inlay tales of Mewar
In the labyrinthine streets of old Udaipur, where time seems to flow like honey, artisans hunch over their workbenches just as their ancestors did centuries ago, their skilled hands fluttering across surfaces of bone, marble, and glass. This ancient craft, which flourished under the patronage of Mewar rulers in the 16th century, transforms ordinary surfaces into extraordinary canvases...
In the labyrinthine streets of old Udaipur, where time seems to flow like honey, artisans hunch over their workbenches just as their ancestors did centuries ago, their skilled hands fluttering across surfaces of bone, marble, and glass. This ancient craft, which flourished under the patronage of Mewar rulers in the 16th century, transforms ordinary surfaces into extraordinary canvases of intricate patterns and storytelling motifs. Today, in workshops tucked away in the shadow of the City Palace, craftsmen preserve this artistic legacy while breathing new life into the tradition. Their designs trace familiar patterns—delicate peacocks, blooming lotus flowers, and geometric mandalas—but now these timeless motifs find themselves at home on modern furniture pieces and contemporary interior installations, blending Udaipur's royal past with its creative present.
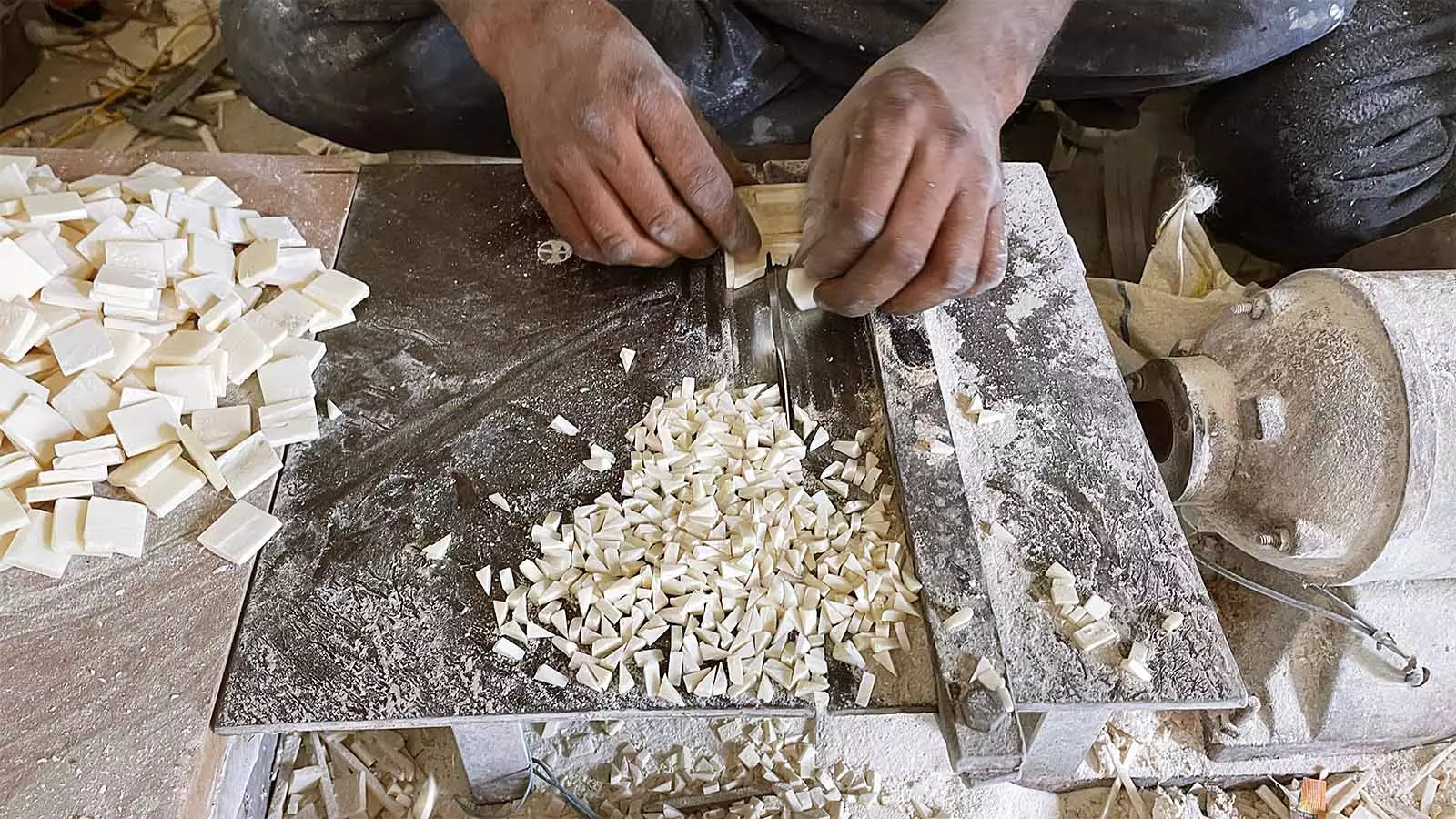
Bone inlay artistry, a tribute to India's decorative genius, emerged from the skilled hands of Udaipur's master craftsmen who transformed humble materials into stunning works of art.
Introduced to India by Mughal Emperor Shah Jahan in the 17th century, Marble inlay flourished under the reign of Jahangir and was perfected by skilled Mughal artisans. “This art closely resembles the Italian Pietra Dura, which was introduced to India through gifts received by the Mughal court. Unlike traditional carving, marble inlay involves a reverse process—cutting the stone to fit a design rather than sculpting the surface itself. It’s an art of subtraction rather than addition,” shares Debosmita Kapse, senior Marcom manager of Sayaji Hotels, who highlights how the art of marble inlay at the newly launched Sayaji Resorts & Spa in Udaipur extends beyond ornamental flooring to adorn décor pieces. “It is prominently featured in decorative panels, cabinet fronts, tabletops, and architectural embellishments, with artisans refining the technique to new heights,” she adds.
Also read | India’s favourite party state is redefining the spirits game
The labour-intensive process begins with artisans conceptualising intricate designs inspired by nature and traditional motifs. Patterns are then carved into a marble base, into which precisely cut and shaped stones are inlaid, and polished for a seamless finish. Historically, artisans have used precious stones like turquoise (Egypt, Persia), coral (Japan, Italy), carnelian (India), amethyst (Brazil, Uruguay, Africa), jade (China), and tiger’s eye (Brazil, Burma, India). Onyx (favoured by Greeks and Romans) and agate (Italy, US, Brazil) also feature prominently. Among the most sought-after base materials is Makrana marble—when unavailable, artisans often substitute black sandstone or green marble.
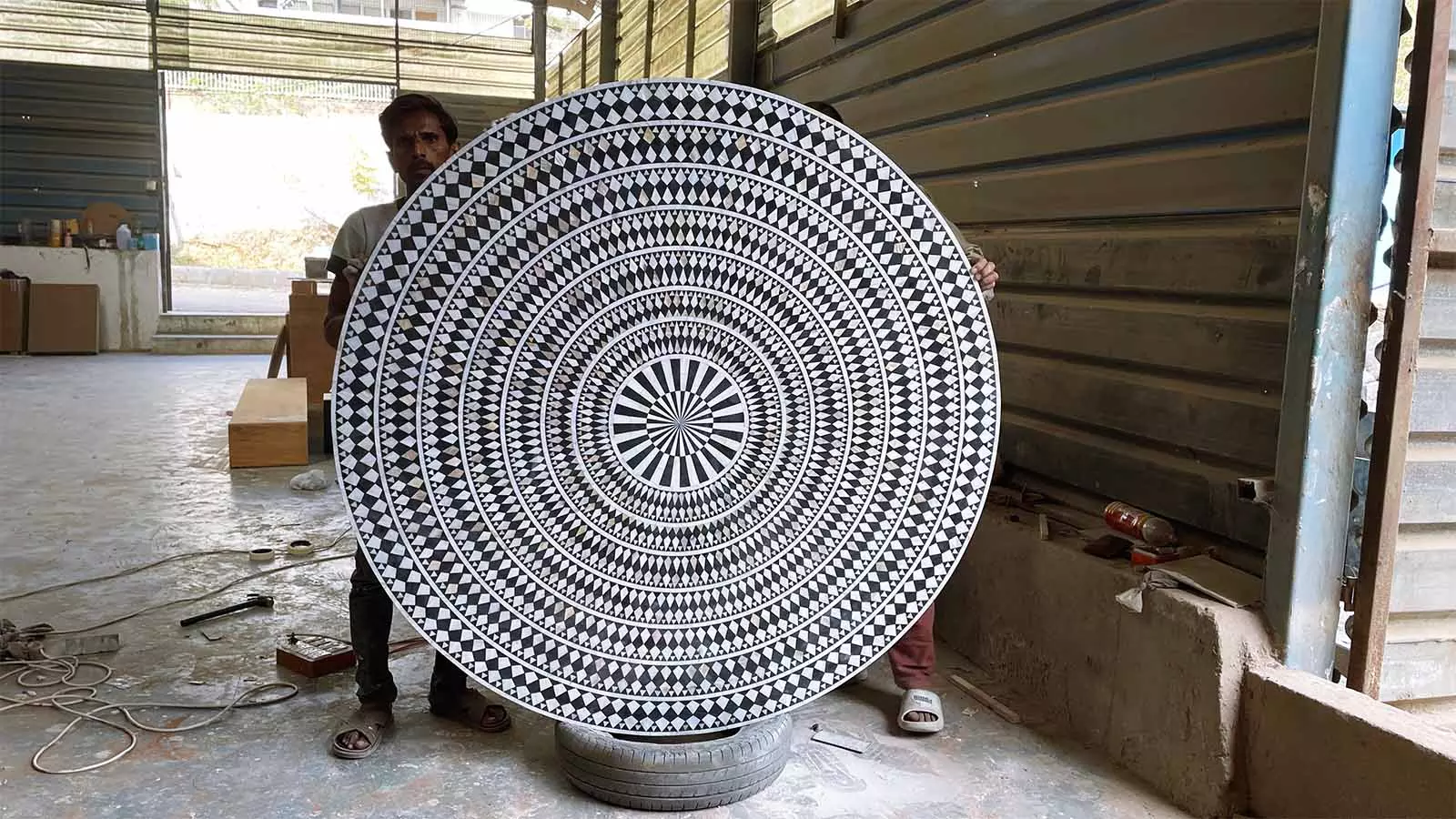
A typical order, such as a large coffee table, takes around 15 days to craft, followed by an additional 10 days for shipping.
“Marble inlay flooring remains a preferred choice for its aesthetic grandeur, and the right patterns, designs, and colours can elevate an interior’s elegance,” Kapse notes. And yet for those seeking a deeper appreciation of Udaipur’s artistic heritage, Kapse recommends exploring the city’s bone and glass inlay work, which continues to reflect its regal legacy. “The City Palace’s Mor Chowk (Peacock Courtyard) stands as a remarkable example,” she says, “with thousands of coloured glass pieces and inlaid stones forming peacock motifs against marble panels, while Udaipur’s palaces and Havelis also showcase exquisite bone and glass inlay work.”
Also read | How Mughal legacy of Taj Mahal is facing an existential crisis
Bone inlay artistry, a tribute to India's decorative genius, emerged from the skilled hands of Udaipur's master craftsmen who transformed humble materials into stunning works of art. Their meticulous technique of setting precisely cut camel bone and mother-of-pearl fragments into wooden surfaces created intricate flowing designs that adorned everything from royal chambers to temples. As this sophisticated craft spread throughout Rajasthan, it became synonymous with refinement and prestige, with aristocratic families commissioning elaborate pieces to showcase both their taste and status.
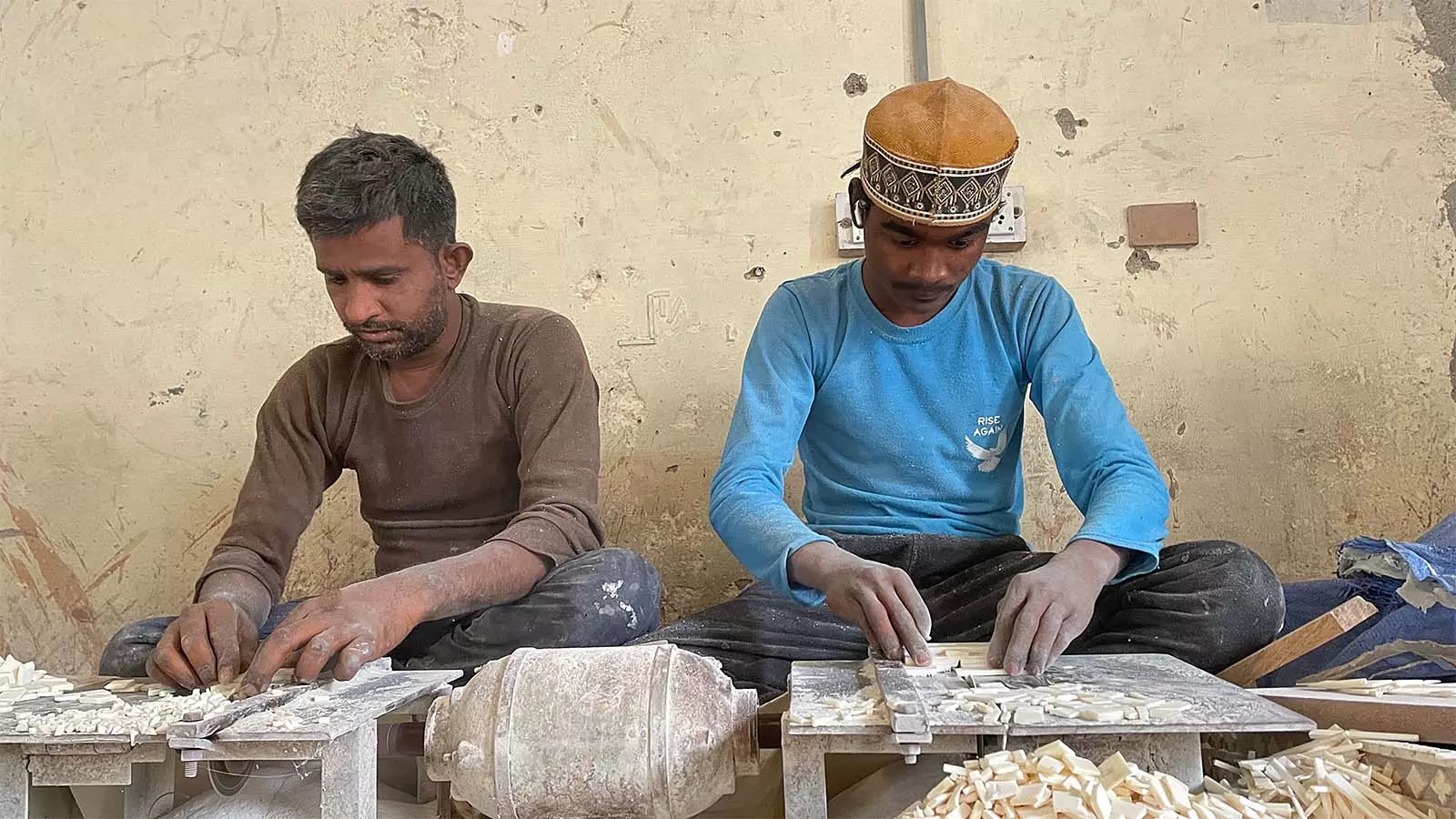
Bone cutting and grinding in process.
In Udaipur’s Bhamashah Industrial Area, young entrepreneurs Chirag Jain and Tej Singh Ahluwati have carved a niche in the world of luxury handicraft. Owners of a boutique in old Udaipur, the duo operates their workshop in Kaladwas, specialising in the bone inlay work for over a decade of experience. Their factory offers a glimpse into the meticulous process—where large batches of bones can be seen sun-drying at the entrance, a crucial step in creating their exquisite designs.
Jain clarifies a common misconception, stating, “These are not camel bones. Camel bones were banned long ago after camels were declared the state animal and are now protected. Instead, we use buffalo bones sourced from Kanpur and other places.” Elaborating on the intricate process, he explains, “It takes around 15 to 20 days to craft a single piece, with a team of two to three artisans working on it. The production involves eight to ten meticulous steps before the final product is ready.”
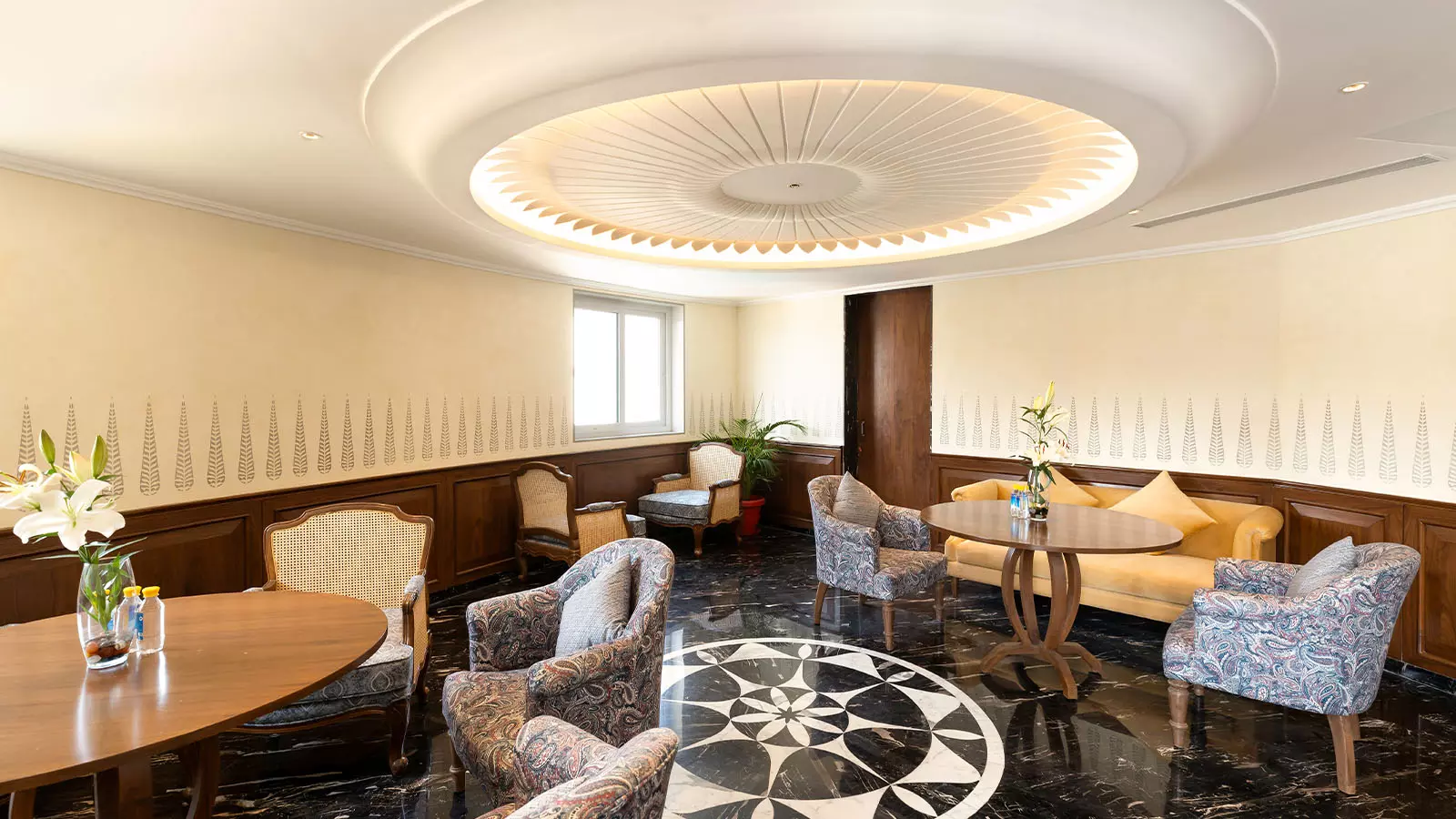
Marble inlay work at Sayaji Resorts & Spa in Udaipur.
The process begins with structuring the base, while the bones—sourced from government-authorized shops—are left to sun-dry for up to five days. Once dried, they undergo a chemical treatment before being cut, ground, shaped, polished, and inserted into the design. The prepared inlays are then carefully pasted onto the wooden structure, followed by resin and epoxy filling to cover the remaining gaps. The final steps involve colouring and finishing, ensuring that every piece remains exquisite.
Also read | How a Guwahati 'chef' fast-tracked Northeast India's street food
The beauty of bone inlay craftsmanship lies in its versatility—it can be custom-made in any colour, shape, or design to suit a client’s preference. However, as Tej Singh Ahluwati explains, “The bones themselves cannot be coloured. Instead, we use a resin mixture made from dolomite, mineral powder, and pigments, allowing us to achieve any shade—pink, black, white, or any other colour requested by the customer to fill the gaps.” Detailing the final stages of production, he adds, “Once the resin is applied, the piece is left to dry for three to four days. After it fully sets, it is carefully sanded using hand tools, grinders, and manually operated sanding machines, bringing out the intricate design.” A typical order, such as a large coffee table, takes around 15 days to craft, followed by an additional 10 days for shipping. “We ship worldwide,” Ahluwati affirms, highlighting their global clientele.
The pricing for these exquisite bone inlay pieces varies based on size and detailing, with bedside tables starting at $500 and larger, more intricate pieces reaching up to $100,000. “We primarily create floral designs, as they represent the rich heritage of Udaipur and Rajasthan,” the duo shares. “Udaipur is particularly known for its floral motifs, so leaves and intricate patterns dominate our designs. However, we also offer customization—if a customer wants their bedsheet print replicated on a table, we can make that happen.” The vision behind 'Luxury Handicrafts' was to make these timeless creations accessible beyond traditional fairs. Today, customers can order directly through their website or WhatsApp. Their clientele extends far beyond India, with exports reaching the USA, Europe, South Africa, and Australia.
As of late, bone inlay furniture has evolved from its origins in royal courts to become a coveted element in contemporary interior design. The technique has found particular resonance in Middle East, where it speaks to a desire for refined, handcrafted luxury in home décor. From small decorative items like tissue holders embellished with mother of pearl to grand statement pieces like detailed cabinets, each bone inlay creation stands as a unique artistic achievement. The process of hand crafting these pieces ensures that no two are exactly alike, making them true collector's items. Just as bone inlay furniture represents the pinnacle of luxurious handcrafted décor, so does the glittering glass inlay, or 'Tikri' work of Udaipur.
Glass inlay is a traditional Indian craft, a tradition that first emerged in the grand halls of Mughal emperors and Rajput rulers. Eventually, this decorative technique, partially influenced by Florence's pietra-dura stonework, became an integral part of South Asian architecture. However, unlike its Italian counterpart, these inlays couldn't exist independently—they are embedded into the very fabric of the buildings, adorning structural elements from plinths to arches. The craft reached its pinnacle during Shahjehan's reign, as evidenced by the dazzling Sheesh Mahal and his ornate throne chamber in Delhi's Red Fort. Over time, this royal art form trickled down to merchant homes, particularly visible in the Shekhavati Havelis built by Marwari traders.
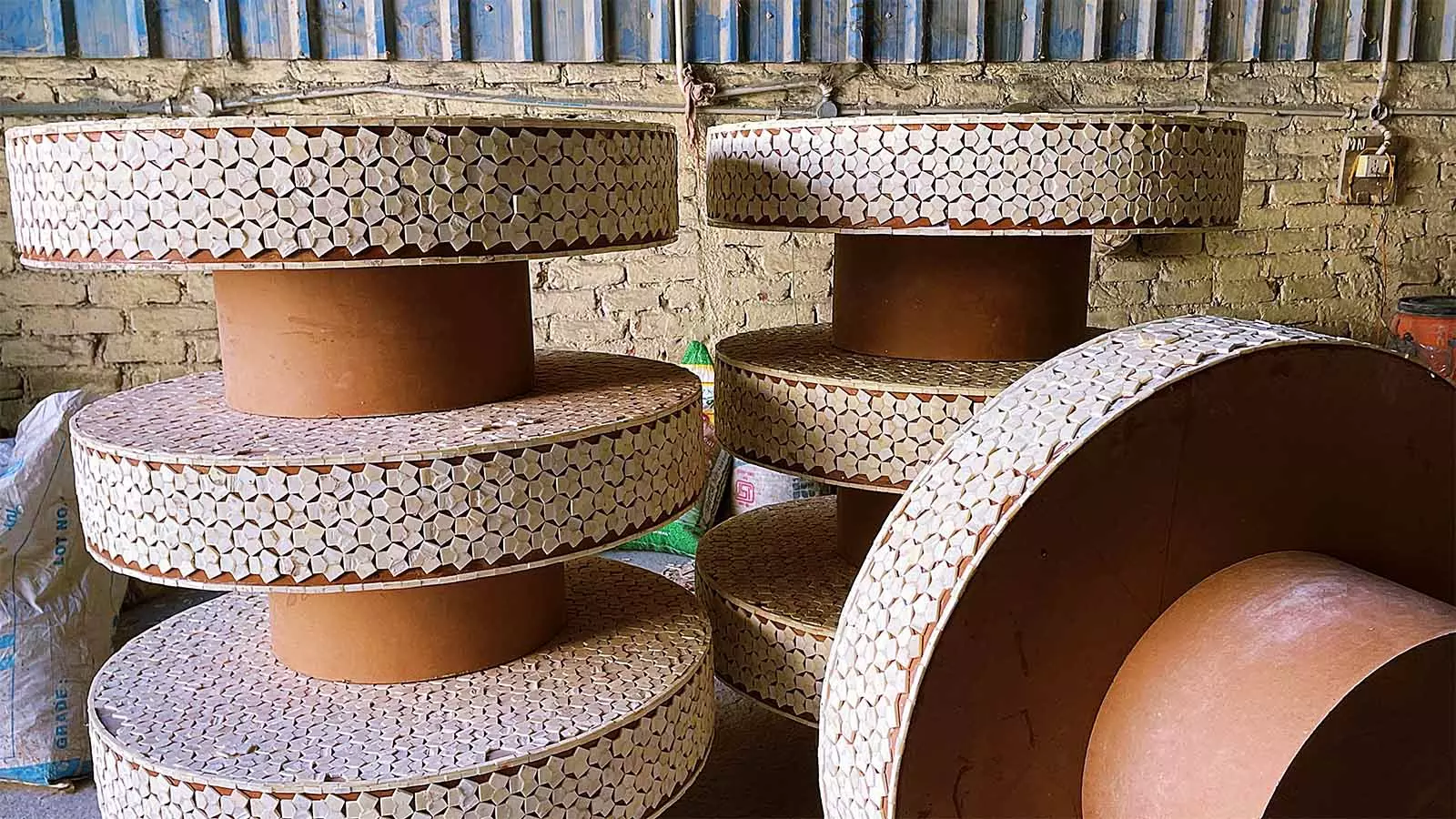
Bone inlay pieces
Located at 15, Bhattiyani Chohatta, Dhaneriya ji ki Haweli near Jal Sanjhi Temple in Jagdish Chowk, the modestly named 'Glass Inlay' has been a cornerstone of the city's architectural heritage for four decades. Originating in Rajasthan, particularly in Udaipur, this decorative technique involves arranging small, colourful glass tesserae (individual pieces) to form intricate designs on various surfaces ranging from walls to tabletops and floors to furniture.
Anant 'Rajesh' Maheshwari, who has spent 40 years restoring glass inlay work in Udaipur's palaces and designing for luxury hotels, explains the craft's royal legacy: “Glass inlay served as a symbol of imperial authority in architecture. In Mughal mausoleums, the intricacy of inlay work indicated the deceased's social status. This art form, perfected during the Mughal period in India, found numerous applications,” he continues, “In Udaipur's winter palaces, it served a particularly ingenious purpose—the mirrors would amplify candlelight, with a single flame multiplied to appear like thousands. Beyond this practical function, the technique added depth to flat walls, transforming ordinary halls into what many described as 'glittering jewel boxes.” The same technique as of Sheesh Mahal was later recreated by Maheshwari for the Bollywood film Prem Ratan Dhan Payo.
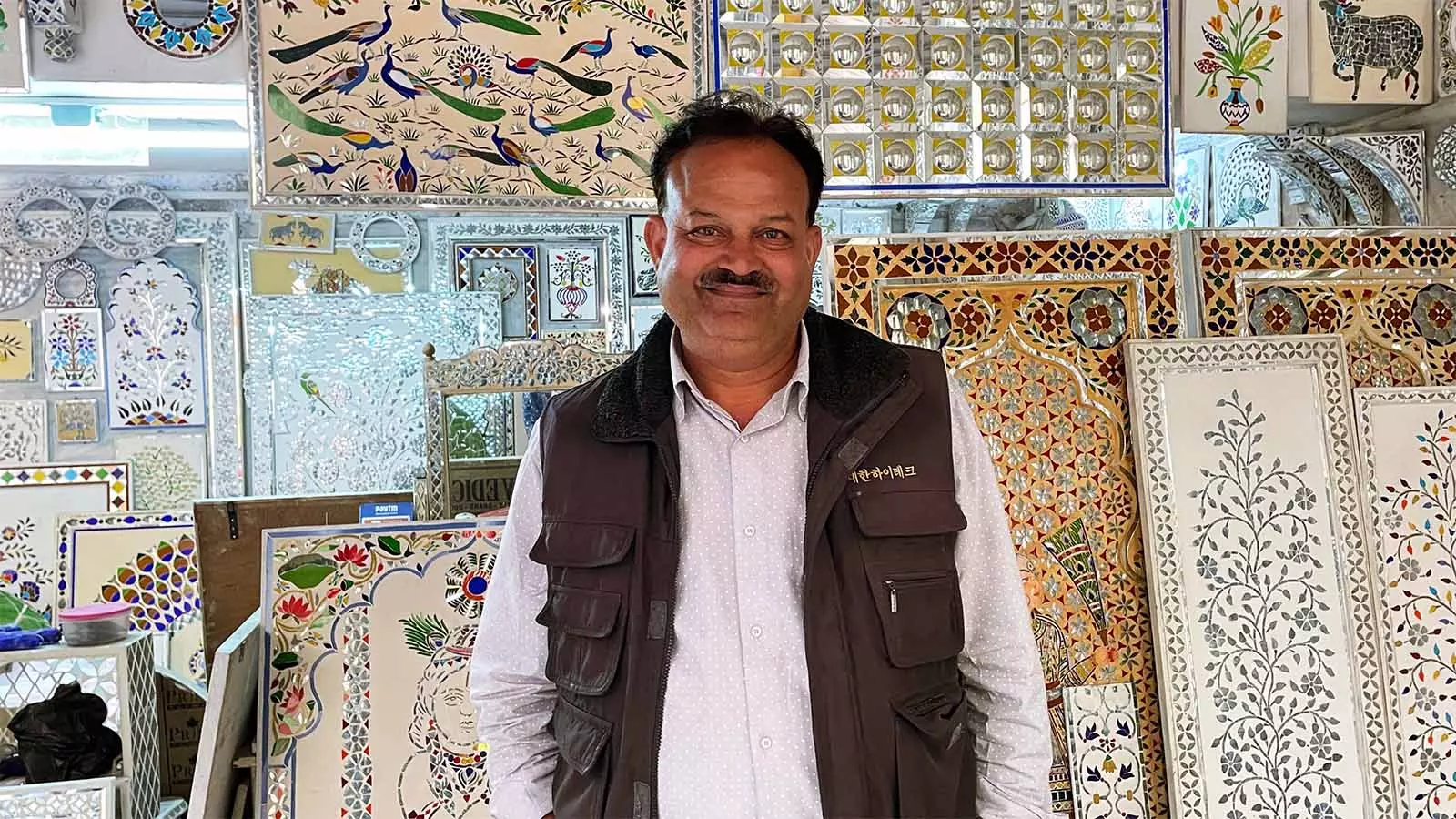
Anant Maheshwari says glass inlay served as a symbol of imperial authority in architecture.
Rajesh says he has been mastering the art of glass inlay since his ninth grade; he now employs around 12 generational craftsmen in his workshop—artisans trained by those who worked on the intricate glass inlay of the City Palace. “We use a 3mm glass known as Belgium glass, though it is not actually from Belgium,” he explains. Creating a single piece of artwork requires the effort of five to six artisans over four days, though the time investment varies depending on the complexity of the design. Prices range from ₹2,500 to ₹3,00,000 for three-dimensional pieces, while larger artworks can take up to two months to complete.
Maheshwari details the intricate process behind glass inlay work, “It all begins with a design, typically featuring floral and leaf motifs, which is outlined on the glass using a pen or watercolour,” he explains. “The glass is then cut with a diamond-tipped tool and shaped using a round stick, followed by a reverse stick for the finer details.” Unlike mirrors, the glass inlay is crafted upside down. When applying it to plywood or walls, a paper is pressed onto the design, which is later removed with water to reveal the final pattern. Given the weight of the glass, we use Guar—a masala, a traditional adhesive made from a blend of ghee and sugar, to hold the pieces in place. Once set and dried, the artwork undergoes polishing to ensure the mirrors are securely and evenly affixed. “Glass inlay work is a versatile and handcrafted art form that brings colour, texture, and elegance to a variety of surfaces and objects,” Maheshwari adds.
Today, this sustainable craft uses local materials and traditional techniques passed down through generations, thrives in the mud-finished walls of village homes across Rajasthan and Gujarat, where artisans hand-place each tiny mirror chip to create intricate patterns of birds, flowers, leaves, and vessels. Beyond its aesthetic value, this handcrafted glass work serves a practical purpose—acting as natural insulation against the region's intense heat. The carefully positioned mirror fragments on exterior walls reflect sunlight away from the building, helping maintain cooler interiors. The art form appears in temples and heritage hotels too, preserving both cultural heritage and environmental wisdom that leave minimal ecological impact while creating lasting beauty.
As master craftsmen like Anant Maheshwari, Chirag Jain, and Tej Singh Ahluwati lead a renaissance, transforming mirrors and bones into breathtaking contemporary installations; their work not only preserves centuries-old craftsmanship but also pushes creative boundaries, creating immersive experiences that bridge the past and present. Through their dedicated artistry, this sustainable, handcrafted tradition not only survives but thrives, proving that ancient wisdom can offer both beauty and practical solutions for our modern world.